Always identify workplace hazards
5 May 2015
The Hawera District Court has ordered two companies to pay fines and reparation totalling $70,000 after a worker fell into a cellar at a mothballed oil and gas facility in Taranaki.
The worker fell 3.2 metres after a grating covering a well cellar gave way while he was standing on it. An internal investigation found that the clips used to secure the grating were missing.
The worker suffered a 7-centimetre cut to his shin and a compression fracture of his spine but managed to climb the escape ladder, even though it had several broken rungs and was coming away from the top of the cellar wall.
The Company, which operates the site in partnership with L&M Energy Limited (which was NOT charged), was fined $30,000 and ordered to pay reparation of $10,000. One company had engaged a sub contracting company to work at the site and the injured man was a contractor engaged by that company. The sub contracting company was also fined $30,000.
The companies were sentenced today in the Hawera District Court under sections 18 and 50 of the Health and Safety in Employment, after earlier pleading guilty.
WorkSafe New Zealand's chief inspector Keith Stewart says a full hazard assessment of the site would have identified the risk posed by the cellar, which has now been filled in.
"Both companies had a duty to identify and manage risks at the site before workers were put in harm's way. A proper assessment would have found that the clips were missing. Given the height of the cellar a second way of securing the grating should also have been in place.
"The company's should also have ensured there was a safe escape route available if someone did fall.
"This incident could have been avoided with a bit more care and attention to risk identification. Once a hazard is identified it is often relatively simple to manage," says Keith Stewart
For more information visit: http://www.business.govt.nz/worksafe/news/releases/2015/always-identify-workplace-hazards
The Hawera District Court has ordered two companies to pay fines and reparation totalling $70,000 after a worker fell into a cellar at a mothballed oil and gas facility in Taranaki.
The worker fell 3.2 metres after a grating covering a well cellar gave way while he was standing on it. An internal investigation found that the clips used to secure the grating were missing.
The worker suffered a 7-centimetre cut to his shin and a compression fracture of his spine but managed to climb the escape ladder, even though it had several broken rungs and was coming away from the top of the cellar wall.
The Company, which operates the site in partnership with L&M Energy Limited (which was NOT charged), was fined $30,000 and ordered to pay reparation of $10,000. One company had engaged a sub contracting company to work at the site and the injured man was a contractor engaged by that company. The sub contracting company was also fined $30,000.
The companies were sentenced today in the Hawera District Court under sections 18 and 50 of the Health and Safety in Employment, after earlier pleading guilty.
WorkSafe New Zealand's chief inspector Keith Stewart says a full hazard assessment of the site would have identified the risk posed by the cellar, which has now been filled in.
"Both companies had a duty to identify and manage risks at the site before workers were put in harm's way. A proper assessment would have found that the clips were missing. Given the height of the cellar a second way of securing the grating should also have been in place.
"The company's should also have ensured there was a safe escape route available if someone did fall.
"This incident could have been avoided with a bit more care and attention to risk identification. Once a hazard is identified it is often relatively simple to manage," says Keith Stewart
For more information visit: http://www.business.govt.nz/worksafe/news/releases/2015/always-identify-workplace-hazards
Don’t be blasé about toxic fumes and confined spaces
16 February 2015
A Waterproofing company has been fined $33,750 and ordered to pay reparation of $2,500 after one of its employees was overcome by toxic fumes.
The worker was applying a bitumen-based product called Novaglass rapid primer to the inside of a grain silo at an egg farm near Hastings at the time of the incident in April 2014. He was wearing a respirator, but did not have a solvent filter available and so used a dust filter. That meant he was exposed to the toxic solvent fumes.
The worker spent more than six hours working by himself on the silo, and was found unconscious and unresponsive on the bottom of the silo near the end of the work day. He was taken to Hawke's Bay Hospital where he was diagnosed as suffering from the toxic effect of carbon monoxide and "other gases, fumes and vapours". He was discharged later that same day.
The waterproofing company pleaded guilty in the Hastings District Court for failing to take all practicable steps to ensure that its employee was not exposed to the hazard of working with solvents in a confined space. The company was charged under sections 6 and 50 of the Health and Safety in Employment Act.
WorkSafe New Zealand's Chief Inspector Keith Stewart says working with toxic chemicals in a confined space is inherently risky.
The company had not trained its employees in working in confined spaces and did not have an operating procedure for such work.
"The company's director admitted that maybe he had "got blasé about the health and safety" because he had experienced staff and had a good health and safety record. Well, you can't afford to get blasé when it comes to working with hazardous chemicals – especially in a confined space.
"In this instance the worker in question escaped without serious, long-term health effects – but that was more a matter of good luck than good management," says Keith Stewart.
For more information visit: http://www.business.govt.nz/worksafe/news/releases/2015/dont-be-blase-about-toxic-fumes-and-confined-spaces
A Waterproofing company has been fined $33,750 and ordered to pay reparation of $2,500 after one of its employees was overcome by toxic fumes.
The worker was applying a bitumen-based product called Novaglass rapid primer to the inside of a grain silo at an egg farm near Hastings at the time of the incident in April 2014. He was wearing a respirator, but did not have a solvent filter available and so used a dust filter. That meant he was exposed to the toxic solvent fumes.
The worker spent more than six hours working by himself on the silo, and was found unconscious and unresponsive on the bottom of the silo near the end of the work day. He was taken to Hawke's Bay Hospital where he was diagnosed as suffering from the toxic effect of carbon monoxide and "other gases, fumes and vapours". He was discharged later that same day.
The waterproofing company pleaded guilty in the Hastings District Court for failing to take all practicable steps to ensure that its employee was not exposed to the hazard of working with solvents in a confined space. The company was charged under sections 6 and 50 of the Health and Safety in Employment Act.
WorkSafe New Zealand's Chief Inspector Keith Stewart says working with toxic chemicals in a confined space is inherently risky.
The company had not trained its employees in working in confined spaces and did not have an operating procedure for such work.
"The company's director admitted that maybe he had "got blasé about the health and safety" because he had experienced staff and had a good health and safety record. Well, you can't afford to get blasé when it comes to working with hazardous chemicals – especially in a confined space.
"In this instance the worker in question escaped without serious, long-term health effects – but that was more a matter of good luck than good management," says Keith Stewart.
For more information visit: http://www.business.govt.nz/worksafe/news/releases/2015/dont-be-blase-about-toxic-fumes-and-confined-spaces
Student gets $30,000 after 10 metre fall
10 November 2014
A Waikato training institute of has been ordered to pay reparation of $30,000 to a student who fell 10 metres during a high ropes course on 24 March 2014. He suffered a fractured pelvis, a compound fracture to the right elbow and lacerations to this right wrist which needed nine stitches. He had surgery on his elbow and spent seven days in hospital. He was also confined to a wheelchair for four weeks after being discharged from hospital because he could not walk.
The institute was sentenced today in the Hamilton District Court after being found guilty of three offences under the Health and Safety and Employment Act, including failing to notify WorkSafe New Zealand that the accident had occurred. The training institute also failed to ensure that the student was not harmed by the actions or inactions of its employee while at work and failed to take all practicable steps to ensure a hazard did not harm the student.
WorkSafe New Zealand's investigation revealed that the fall arrest ropes used by the victim during the class had been incorrectly attached to a thin plastic link on the rear of the chest harness by an unsupervised student. The karabiners were also not hooked through the webbing of both the chest harness and the seat harness.
“While multiple health and safety failings led to this incident, it is unacceptable that an instructor asked a student to fit a harness and then left him on his own to do it without supervision," says Keith Stewart, WorkSafe New Zealand's Chief Inspector.
“The institute had also not assessed the instructor's competence to teach the high ropes course or provided them with any professional development so they could keep up with industry standards. They also did not have a functional health and safety management system in place at the time of the incident.
“Any high ropes course has a serious risk of fall from heights so it's crucial that health and safety practices are a priority."
For more information visit: http://www.business.govt.nz/worksafe/news/releases/2014/student-gets-30-000-after-10-metre-fall
A Waikato training institute of has been ordered to pay reparation of $30,000 to a student who fell 10 metres during a high ropes course on 24 March 2014. He suffered a fractured pelvis, a compound fracture to the right elbow and lacerations to this right wrist which needed nine stitches. He had surgery on his elbow and spent seven days in hospital. He was also confined to a wheelchair for four weeks after being discharged from hospital because he could not walk.
The institute was sentenced today in the Hamilton District Court after being found guilty of three offences under the Health and Safety and Employment Act, including failing to notify WorkSafe New Zealand that the accident had occurred. The training institute also failed to ensure that the student was not harmed by the actions or inactions of its employee while at work and failed to take all practicable steps to ensure a hazard did not harm the student.
WorkSafe New Zealand's investigation revealed that the fall arrest ropes used by the victim during the class had been incorrectly attached to a thin plastic link on the rear of the chest harness by an unsupervised student. The karabiners were also not hooked through the webbing of both the chest harness and the seat harness.
“While multiple health and safety failings led to this incident, it is unacceptable that an instructor asked a student to fit a harness and then left him on his own to do it without supervision," says Keith Stewart, WorkSafe New Zealand's Chief Inspector.
“The institute had also not assessed the instructor's competence to teach the high ropes course or provided them with any professional development so they could keep up with industry standards. They also did not have a functional health and safety management system in place at the time of the incident.
“Any high ropes course has a serious risk of fall from heights so it's crucial that health and safety practices are a priority."
For more information visit: http://www.business.govt.nz/worksafe/news/releases/2014/student-gets-30-000-after-10-metre-fall
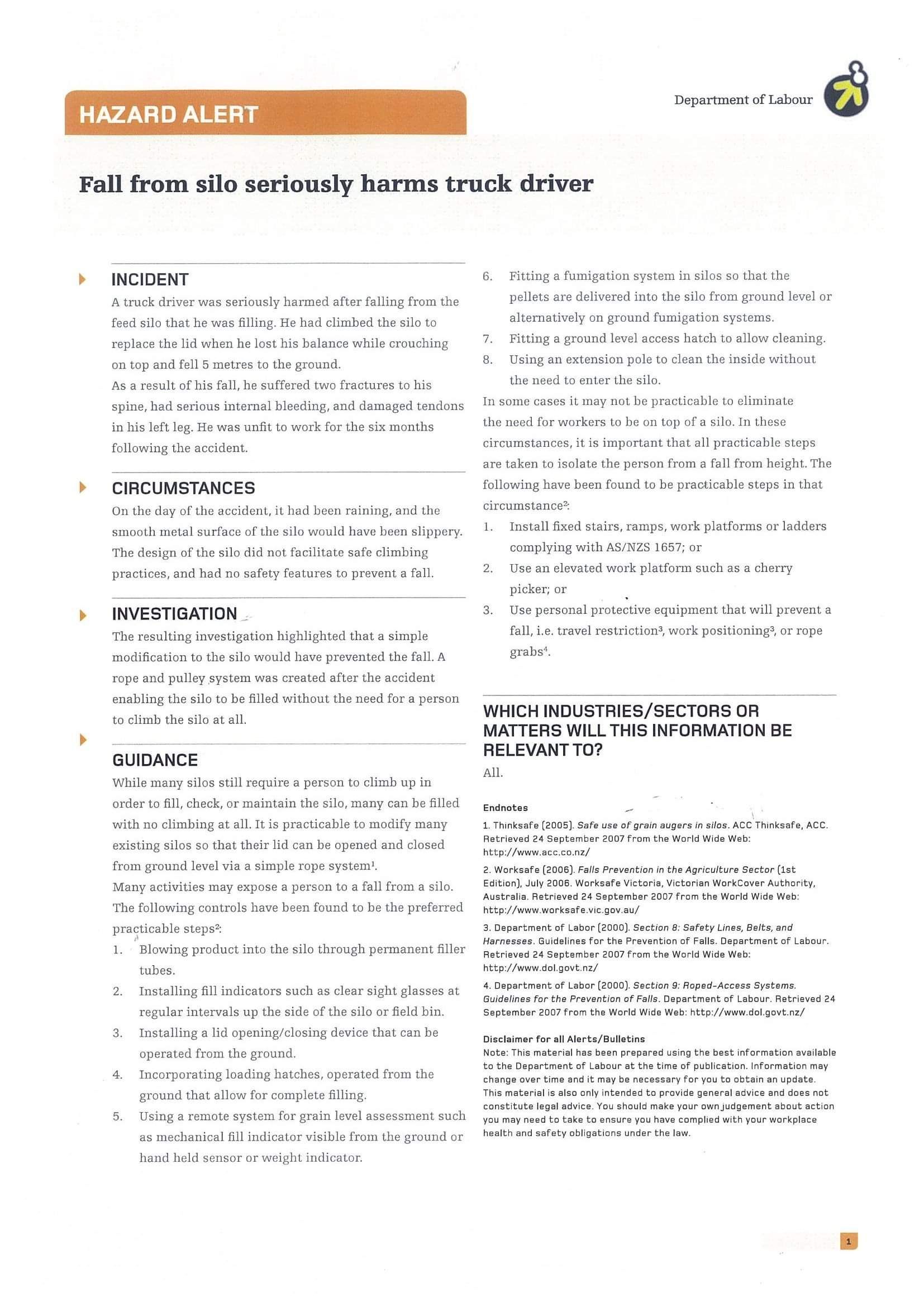
Safety gear no good if it is not used
29 September 2014
A Roofing company has been fined $45,000 and ordered to pay reparation of $3,000 after one of its employees fell from a height of 2.5 metres.
An employee was screwing down roofing iron at a kindergarten in Marton when he stepped backwards and fell. He suffered a severed tendon and cuts to his wrist after coming into
contact with a sheet of iron that had been cut and bent upwards to allow roof flashings to be attached. He was hospitalised for two days and was off work for two and a half months.
At the time of the fall the employee and the company director were both wearing safety harnesses, but neither had been attached to an anchor point. In addition, edge protection had been delivered to the site but had not been installed.
This roofing company was sentenced today in the Wanganui District Court under the Health and Safety in Employment Act for failing to take all practicable steps to ensure the safety of an employee.
WorkSafe New Zealand’s Chief Inspector Keith Stewart says there is simply no excuse for not using proper safety equipment – particularly when it is readily to hand.
“It beggars belief that these two were both wearing a safety harness but they weren’t secured. When the director was asked why they were not attached he replied ‘I just got lazy’. That’s not good enough.
“Working at height is always risky. Both the harnesses and the edge protection should have been used.
“Safety gear is no good to anyone if it’s not being used,” says Keith Stewart.
For more information with regards to this story visit: http://www.business.govt.nz/worksafe/news/releases/2014/safety-gear-no-good-if-it-is-not-used
A Roofing company has been fined $45,000 and ordered to pay reparation of $3,000 after one of its employees fell from a height of 2.5 metres.
An employee was screwing down roofing iron at a kindergarten in Marton when he stepped backwards and fell. He suffered a severed tendon and cuts to his wrist after coming into
contact with a sheet of iron that had been cut and bent upwards to allow roof flashings to be attached. He was hospitalised for two days and was off work for two and a half months.
At the time of the fall the employee and the company director were both wearing safety harnesses, but neither had been attached to an anchor point. In addition, edge protection had been delivered to the site but had not been installed.
This roofing company was sentenced today in the Wanganui District Court under the Health and Safety in Employment Act for failing to take all practicable steps to ensure the safety of an employee.
WorkSafe New Zealand’s Chief Inspector Keith Stewart says there is simply no excuse for not using proper safety equipment – particularly when it is readily to hand.
“It beggars belief that these two were both wearing a safety harness but they weren’t secured. When the director was asked why they were not attached he replied ‘I just got lazy’. That’s not good enough.
“Working at height is always risky. Both the harnesses and the edge protection should have been used.
“Safety gear is no good to anyone if it’s not being used,” says Keith Stewart.
For more information with regards to this story visit: http://www.business.govt.nz/worksafe/news/releases/2014/safety-gear-no-good-if-it-is-not-used
No excuse for failing to reduce risk of falls
10 September 2014
An Auckland company has been fined $30,000 and ordered to pay reparation of $10,000 after an employee of a sub-contractor fell from a height of five metres.
The employee suffered multiple fractures and significant head injuries after the fall in August 2013, and suffers ongoing medical effects including headaches and amnesia. The employee was installing the supporting frame for the roof of a new retirement home in Albany when he stepped on a piece of timber that had yet to be fixed down, causing
him to fall five metres onto the concrete floor below. Fall protection equipment including mobile scaffolds, a scissor lift and thirty ‘fall arrest’ bean bags were available at the site,
but was not being used.
The Construction was convicted in the North Short District Court and sentenced yesterday under sections 18 and 50 of the Health and Safety in Employment Act for failing to take all practicable steps to ensure their employee was not harmed at work.
WorkSafe New Zealand’s Programme Manager Construction and Manufacturing, Marcus Nalter, says the construction company should have ensured that the fall protection equipment that was provided was used.
This construction company had verbally advised that the scissor lift and bean bags should be used while work was being done on the upper area of the roof trusses. But it did not ensure that the sub-contractor’s fall protection controls were properly documented or that the risk analysis for the task was reviewed, updated and followed.
"Falls from height are one of the most common causes of serious injuries in construction. There is simply no excuse for construction companies not to ensure there is a proper plan in place to minimise the risk of falls," says Marcus Nalter.
For more information with regards to this story visit:
http://www.business.govt.nz/worksafe/news/releases/2014/no-excuse-for-failing-to-reduce-risk-of-falls
An Auckland company has been fined $30,000 and ordered to pay reparation of $10,000 after an employee of a sub-contractor fell from a height of five metres.
The employee suffered multiple fractures and significant head injuries after the fall in August 2013, and suffers ongoing medical effects including headaches and amnesia. The employee was installing the supporting frame for the roof of a new retirement home in Albany when he stepped on a piece of timber that had yet to be fixed down, causing
him to fall five metres onto the concrete floor below. Fall protection equipment including mobile scaffolds, a scissor lift and thirty ‘fall arrest’ bean bags were available at the site,
but was not being used.
The Construction was convicted in the North Short District Court and sentenced yesterday under sections 18 and 50 of the Health and Safety in Employment Act for failing to take all practicable steps to ensure their employee was not harmed at work.
WorkSafe New Zealand’s Programme Manager Construction and Manufacturing, Marcus Nalter, says the construction company should have ensured that the fall protection equipment that was provided was used.
This construction company had verbally advised that the scissor lift and bean bags should be used while work was being done on the upper area of the roof trusses. But it did not ensure that the sub-contractor’s fall protection controls were properly documented or that the risk analysis for the task was reviewed, updated and followed.
"Falls from height are one of the most common causes of serious injuries in construction. There is simply no excuse for construction companies not to ensure there is a proper plan in place to minimise the risk of falls," says Marcus Nalter.
For more information with regards to this story visit:
http://www.business.govt.nz/worksafe/news/releases/2014/no-excuse-for-failing-to-reduce-risk-of-falls
Company fined after worker falls from roof
30 January 2014
A Tauranga residential property construction company has been fined $25,000 and ordered to pay reparations of $5000 after a worker was injured in a fall from the roof of a property under construction.
The company was sentenced in the Tauranga District Court today on one charge under the Health and Safety in Employment Act of failing to take all practicable steps to ensure that a contractor was not harmed while doing work he was engaged to do.
The worker fell from the roof of a garage being constructed in Tauriko, Tauranga in April last year. He was assisting others secure a truss to the top plate of the garage when it slipped and the victim lost his balance and fell approximately three metres to the concrete floor of the garage. He sustained fractures to his left wrist and jaw.
“There was no effective means of fall protection in place at this workplace, and had there been, this worker may not have been injured,” Chief Inspector Investigations Keith Stewart said.
“There is no excuse for any construction company not knowing its responsibility to make working at height safe – WorkSafe NZ (and its predecessors) has been running a wide and very active campaign to reduce injuries and deaths from falls from heights.
“There is an Approved Code of Practice for working at height that is widely available and every construction company, whether working in the commercial or residential sectors,should be working to its terms.
“This worker and his colleagues were unnecessarily exposed to dangerous working conditions, and it is fortunate that the victim did not suffer more serious injuries,” Mr Stewart said.
For more information with regards to this story visit:
http://www.business.govt.nz/worksafe/news/releases/2014/company-fined-after-worker-falls-from-roof
A Tauranga residential property construction company has been fined $25,000 and ordered to pay reparations of $5000 after a worker was injured in a fall from the roof of a property under construction.
The company was sentenced in the Tauranga District Court today on one charge under the Health and Safety in Employment Act of failing to take all practicable steps to ensure that a contractor was not harmed while doing work he was engaged to do.
The worker fell from the roof of a garage being constructed in Tauriko, Tauranga in April last year. He was assisting others secure a truss to the top plate of the garage when it slipped and the victim lost his balance and fell approximately three metres to the concrete floor of the garage. He sustained fractures to his left wrist and jaw.
“There was no effective means of fall protection in place at this workplace, and had there been, this worker may not have been injured,” Chief Inspector Investigations Keith Stewart said.
“There is no excuse for any construction company not knowing its responsibility to make working at height safe – WorkSafe NZ (and its predecessors) has been running a wide and very active campaign to reduce injuries and deaths from falls from heights.
“There is an Approved Code of Practice for working at height that is widely available and every construction company, whether working in the commercial or residential sectors,should be working to its terms.
“This worker and his colleagues were unnecessarily exposed to dangerous working conditions, and it is fortunate that the victim did not suffer more serious injuries,” Mr Stewart said.
For more information with regards to this story visit:
http://www.business.govt.nz/worksafe/news/releases/2014/company-fined-after-worker-falls-from-roof
Grain silo operator fined for worker injury
20 August 2013
A worker who was seriously injured in a grain silo accident in October last year has been awarded $26,000 in emotional harm reparations and his employer fined $35,000.
The company had already paid nearly $20,000 to the victim. The company had previously pleaded guilty to one charge (Section 6) under the Health and Safety in Employment Act 1992 and was sentenced at the Manukau District Court today.
The victim was asked by his supervisor to sweep remaining grain from a silo before a new delivery. The silo contains a sweep auger which operates when gravity no longer forces the grain out of the silo, but which leaves a 10 centimetre residue of grain that has to be swept out by hand. The victim knew he was supposed to turn off the auger before entering the silo, but had been shown by a supervisor how to slow the auger and sweep out the silo when it was operating at slow speed. This method was not authorised by the company he worked for.
He fell into the moving auger blades suffering a head injury, fractures to his right arm, right lower leg, right eye socket and jaw as well as broken tendons in one leg and extensive bruising. “The victim did not comply with company procedures, but the company had not isolated the hazard by installing an interlock which would have locked the silo access door while the auger was still active,” the Chief Inspector Investigations for the Health and Safety group Keith Stewart said. “This would have ensured workers could not over-ride company instructions by slowing the auger and working in a dangerous environment,” Mr Stewart said.
For more information with regards to this story visit:
http://www.business.govt.nz/worksafe/news/releases/2013/grain-silo-operator-fined-for-worker-injury
The company had already paid nearly $20,000 to the victim. The company had previously pleaded guilty to one charge (Section 6) under the Health and Safety in Employment Act 1992 and was sentenced at the Manukau District Court today.
The victim was asked by his supervisor to sweep remaining grain from a silo before a new delivery. The silo contains a sweep auger which operates when gravity no longer forces the grain out of the silo, but which leaves a 10 centimetre residue of grain that has to be swept out by hand. The victim knew he was supposed to turn off the auger before entering the silo, but had been shown by a supervisor how to slow the auger and sweep out the silo when it was operating at slow speed. This method was not authorised by the company he worked for.
He fell into the moving auger blades suffering a head injury, fractures to his right arm, right lower leg, right eye socket and jaw as well as broken tendons in one leg and extensive bruising. “The victim did not comply with company procedures, but the company had not isolated the hazard by installing an interlock which would have locked the silo access door while the auger was still active,” the Chief Inspector Investigations for the Health and Safety group Keith Stewart said. “This would have ensured workers could not over-ride company instructions by slowing the auger and working in a dangerous environment,” Mr Stewart said.
For more information with regards to this story visit:
http://www.business.govt.nz/worksafe/news/releases/2013/grain-silo-operator-fined-for-worker-injury